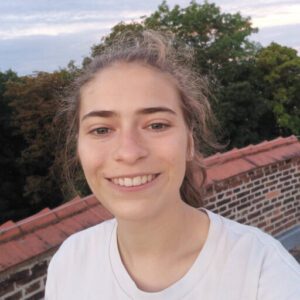
Cooling next generation aircraft with Phase Change Materials: modelling of novel concept heat exchanger designs
E001
Abstract
The growing thermal demand in aircraft design poses significant challenges for developing thermal management systems (TMS) in next-generation aircraft. Phase Change Materials (PCM) absorb and release heat at almost constant temperature and can be used to reduce temperature fluctuations at key stages of the flight, so that a reduction in size of other components could be achieved. PCMs have been successfully applied in various cooling application including for the insulation of buildings and the cooling of refrigeration units, but there is a lack of literature dedicated to the integration of PCMs into heat exchanger geometries for aerospace applications. The loading profile for aerospace favours a reduction of the melting time and the mass of the system in exchange for a higher allowable pressure drop so that more compact PCM heat exchanger geometries are needed. This can be achieved by increasing the surface area between the PCM and the heat transfer fluid. For aerospace applications, a plate-fin heat exchanger can be used as a base geometry, where the finned layers of PCM are separated from the fluid layer with plates.
Computational Fluid Dynamics (CFD) emerges as a powerful tool for accurately modelling the phase change and predicting the thermohydraulic performance of heat exchangers. In this work, a CFD model will be used to study the effect of different fin geometries on the melting of PCM in adjacent layers as well as the hydraulic performance of the heat exchanger. For this purpose, a conjugate heat transfer model of the PCM Compact Heat Exchanger geometries was developed, where the phase change was captured by using an enthalpy-porosity source term.